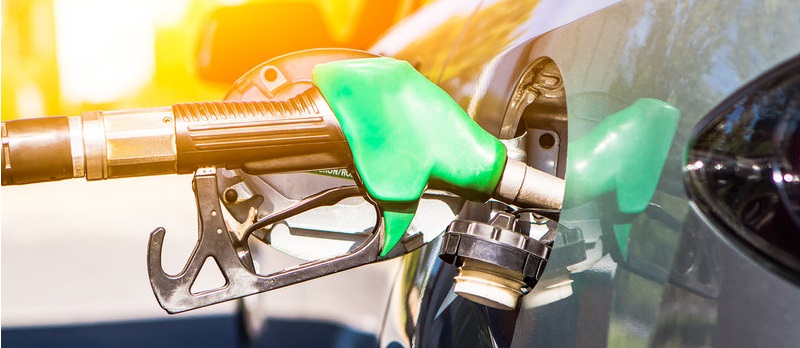
The Concept of Poka Yoke
Have you ever mistakenly try to fill your tank with diesel fuel only to realise the pump didn’t fit?
What saved your car is Poka Yoke: Failure-proof design.
Poka Yoke is a Japanese phrase that simply means making something ‘fail safe’ or mistake proof. Poka Yoke was devised within the Toyota Production System when it was originally defined as being ‘baka yoke’ which in English can be translated as idiot proof or foolproof.
However, after it began to be used, it was then changed to Poke Yoke, meaning mistake proof.
Poka Yoke is central to the concept of ‘Lean’ thinking, which aims to reduce waste and make sure that everything and every process is as efficient as possible.
Poka Yoke In Action
Poka Yoke is any process that can stop mistakes being created, thereby ensuring that there are no defects or errors within the production process. So if a machine is designed to stop or at least sound a warning signal if it is not aligned correctly then this is ‘Poka Yoke’ in action. The operator will be alerted to the fact that the machine has not been correctly aligned and instead of faulty goods being created, or the machine continuing and then perhaps breaking down the operator will take the necessary steps to ensure that the problem is resolved before the faulty goods are created or before the machine breaks down.
This concept of stopping defects or mistakes from happening is central to Poka Yoke thinking. It is not about rectifying mistakes or defects; it is about ensuring that they simply do not happen.
How can poka yoke improve business?
Poka yoke can be easily utilized in your business. It can be implemented with a variety of simple instruments like warning devices, notifications, paper, fixtures, and so on. They serve as preventive measures to prevent people and machines from conducting mistakes. These devices should be easy to install, provide instant prevention and feedback, can function independently, and can be used by everyone.
A poka yoke presentation would reveal that unlike conventional inspection techniques, the practice does not cause any delay in the manufacturing process. Since it falls under the lean manufacturing methodology, little time is needed to ensure each product is free from defects. Given its time-saving capability, It causes a business to be more productive.
Employees engaging in a poka yoke presentation and applying the concepts in their task encourage them to consistently solve problems and make quality products. Plus, It enforces employees to be effective workers, preventing errors and getting zero defects. What does this mean? The need or the rate for reworking and repairing products is drastically reduced. Having faulty products represent waste and errors that could’ve been easily avoided. The objective of this is to constantly satisfy the customer at a minimum cost and with no waste.
Can software help failure-proof your business?
As a business owner, it’s important to find tools to save time, become more productive but specially to reduce or eliminate costly mistakes.
In its own way, our business management software help you achieve exactly that:
- Have visual aids to see if your stocks are in correct availabilities or if you are spending too much time on a specific task or project;
- Automatically suggest other products that are low in inventory when you order to given supplier;
- Avoid common human mathematical errors when duplicating an invoice or a project;
- Automatically sequencing tasks in term of priority to keep your team’s focus on what is actually important;
- And of course, much, much more…